II.
Les diverses valorisations
I. 1. Quest-ce
que la valorisation ?
Il sagit de la fabrication dun produit dérivé des
déchets pour le réintroduire dans les circuits économiques pour des usages,
énergétiques ou de matières premières secondaires.
La valorisation représente la seule solution pour éviter une
accumulation de déchets plastiques dans les décharges. Ceux-ci possèdent en effet une
mauvaise image : ils ont une durée de vie de plusieurs centaines dannées
avant de se dégrader, et ils posent un problème esthétique important : la vue de
sacs de supermarché flottant au vent a marqué les esprits et fait prendre conscience de
la nécessité de les éliminer.
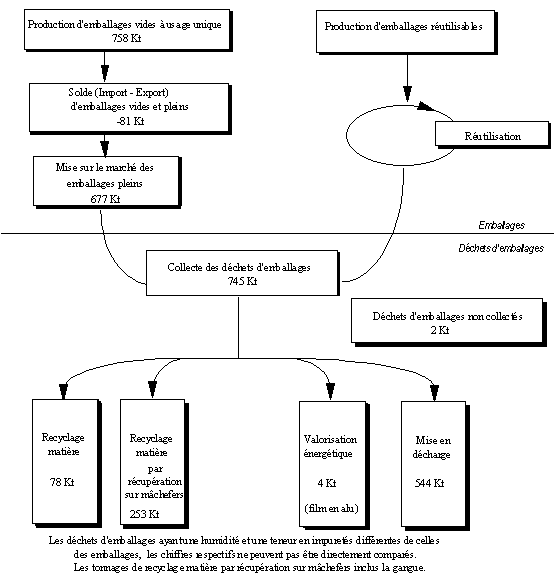
Représentation de la part
des différentes solutions pour le recyclage.
Se pose alors le problème de la solution à
adopter : réutilisation ou élimination ?
I. 2. La
valorisation matière
La réutilisation consiste à transformer les rejets plastiques en
produits moulés de second choix. Cette solution a un but économique clairement affiché,
car elle permet de confier à des entreprises le traitement des déchets plastiques et
leur valorisation.
Le principal processus de valorisation matière ou
réutilisation est la régénération. Elle comporte différents volets :
Le recyclage interne est
une opération couramment pratiquée par les transformateurs de thermoplastiques opérant
sur des procédés de plastification (injection, extrusion, soufflage, calandrage). Elle a
donc lieu en amont du processus de fabrication.
Les chutes et les rebuts propres sont systématiquement
récupérés, par type de polymère, et seront après rebroyage utilisés en mélange avec
de la matière vierge ( 10 à 20 % de matière recyclée ).
La régénération physique
utilise surtout des déchets provenant de producteurs de polymères de base, de
transformation de semi-produits ne disposant pas de système de fabrication, de gros
utilisateurs et des utilisateurs finaux de produits de grande consommation.
Ce procédé comporte différents étapes :
I. 2. 1 le tri
Il seffectue par type de polymère, car ceux-ci ne peuvent
être traités ensemble, et par type dobjet.
Sont concerné par ce tri les flacons, bouteilles et bidons.
I. 2. 2 la
régénération proprement dite
Le but est de retrouver les résines plastiques qui vont permettre
dobtenir des matières premières destinées à lindustrie du recyclage. Elle
est composée de différentes étapes : le lavage, le broyage et la granulation (ou
micronisation selon les cas ).
I. 2. 3 le recyclage
Il sagit dutiliser les résines régénérées (
poudres, granulats, paillettes ) pour fabriquer les produits secondaires.
Ø Le
remoulage est une variante de la régénération
physique , dans laquelle on part dun mélange de polymères différents.
Statistiquement, le PE domine et joue le rôle de liant lorsquon coule par gravité
la matière malaxée et fondue dans un moule ( comme en fonderie ). On compense
laffaiblissement des caractéristiques mécaniques du produit ainsi obtenu par une
forte épaisseur (doù un cycle assez long ).
Ø Une
autre méthode est tout simplement de presser les
déchets plastiques mêlés sous température, la fusion locale les associe,
permettant de produire par exemple des panneaux disolation phonique peu onéreux.
Exemples de valorisation matière :
|
Source |
Seconde vie |
Polyéthylène
(PE) |
Bouteilles
alimentaires (lait
),
flacons de détergents |
Flacons, films
plastiques sacs
poubelles, bacs, canalisations
|
Polyéthylène
Téréphtalate (PET) |
Bouteilles
deau minérale
et de boissons gazeuses |
Vêtements,
rembourrage, fibres pour non tissés techniques
|
Polypropylène
(PP) |
Batteries,
pare-chocs
|
Conteneurs,
corbeilles, revêtements de sol, batteries, pare-chocs
|
Polychlorure de
vinyle (PVC) |
Industrie du
bâtiment (fenêtres, portes, canalisations...) |
Canalisations,
revêtements de sols et muraux, écran antibruit, gaines de câbles, vêtements
|
La recherche progresse dans le domaine de la valorisation matière
et les industriels ont compris limportance de ses applications.
Ainsi , le producteur de fibres Rhovyl et le chimiste
ElfAtochem ont mis au point au milieu des années 90 des fibres dont la particularité est
dêtre fabriquées à partir de bouteilles deau minérale recyclées. Le
procédé de fabrication est simple. Les bouteilles deau arrivent à lusine
sous forme de copeaux, et lune des premières opérations consiste à les dissoudre
grâce à un mélange de solvants. La pâte ainsi obtenue passe ensuite à travers une
filière à trous microscopiques pour former les filaments. Enfin, par différents
traitements thermiques et mécaniques, ces filaments sont transformés en fibres textiles.
Ainsi ces sociétés sont en mesure de commercialiser aujourdhui des chandails de
différents modèles.
Par exemple, il faut en moyenne 27 bouteilles deau minérale
pour faire un pull-over.
Le coût de ces polymères recyclés était en 1997 supérieur à
celui des pull-overs fabriqués à partir de fibres neuves. Mais les deux sociétés
entendent bien abaisser ce prix et développer leur gamme avec la production de
chaussettes ou de sous-vêtements en fibres recyclées.
Comme montré dans le tableau ci-dessus, les fabricants de tuyaux et
canalisations utilisent de plus en plus des plastiques de seconde main en
recourant aux techniques des multicouches. Des câbles sont enrobés dans des gaines
intégrant des plastiques secondaires.
Mais dans lensemble, une bonne partie des plastiques de
collecte recyclés trouvent des débouchés bien plus banals. On les retrouve ainsi
souvent cantonnés à des emplois de substitution du bois.
I. 2. 4 La
valorisation matière en fonction des types de polymère
I. 2. 4. 1 Le cas
des thermoplastiques
Ils réagissent sous leffet de la chaleur, fondent et se
solidifient réversiblement. Le seul problème important quils posent est quil
faut absolument les trier avant de les retraiter. Ils ont en effet des types de
comportement viscoélastique très différents de lun à lautre, et le
mélange obtenu après recyclage possède des propriétés trop dégradées.
Par exemple, le PET et le PVC, qui entrent tous les deux dans la
composition des bouteilles plastiques, sont incompatibles.
I. 2. 4. 2 Le cas
des thermodurcissables
Lorsquils sont mélangés à des fibres (fibre de verre), ils
forment des composites. Par définition infusibles, ils ne peuvent être régénérés. Pour ces deux produits, qui représentent 20 % du
tonnage des plastiques, la valorisation est difficile. Ils peuvent cependant être
utilisés comme charges.
I. 2. 5 Les limites
de la valorisation matière
La principale limite est de nature économique : les coûts de
régénération sont souvent voisins de ceux des polymères vierges pour les plastiques de
grande diffusion, doù une rentabilité aléatoire. De plus, la gestion de flux de
matières dâges et dusages différents complexifie le problème.
Ces contraintes économiques doivent satisfaire plusieurs
conditions :
Ø Disposition
dun gisement de déchets constant en quantité, qualité et prix.
Ø Assurance
dun tri préalable, ce qui suppose de former des opérateurs, de marquer les
polymères par leur symbole respectif, ou mieux de leur inclure un marqueur radioactif.
Ø Utilisation
dun procédé de retraitement économiquement rentable : pour
linvestisseur privé dune part, pour la collectivité dautre part.
Ø Les
produits doivent présenter un rapport prix-performances intéressant et satisfaire un
marché mesurable.
I. 3. La valorisation énergétique (incinération des déchets)
Ce recyclage permet de réduire le volume des déchets et de
récupérer lénergie dégagée lors de la combustion. Cette énergie est ensuite
transformée pour produire de la chaleur et de lélectricité.
Les déchets sont brûlés dans un four alimenté en air. Cette
énergie peut servir à alimenter un « réseau de chaleur » (un réseau de
tuyaux dans lesquels circule de leau chaude qui alimente des habitations en eau
chaude et en chauffage). Elle peut également servir à produire de lélectricité
grâce à des turbines et à des alternateurs.
La valorisation énergétique représente aujourd'hui la voie de
valorisation la plus importante en tonnage pour les déchets d'emballages plastiques. Le
haut pouvoir calorifique des matières plastiques permet d'expliquer ce type de
valorisation. Le tableau suivant présente le PCI des polymères les plus courants ainsi
que celui d'autres matériaux et matières en comparaison :
MATERIAU
- MATIERE |
PCI
Matériau pur (en MJ/kg) |
PCI
Déchets (en MJ/kg) |
PS |
46 |
20 |
PE |
46 |
22 |
PET |
45 |
13 |
PP |
44 |
12 |
PVC |
20 |
|
Fioul
domestique |
44 |
|
Aluminium
fin |
31 |
|
Houille |
29 |
|
Papier-Carton |
17 |
|
Bois |
16 |
|
Ordures
ménagères |
|
8 |
Bien que le PCI des déchets
d'emballages plastiques soit nettement inférieur à celui des polymères purs , leur
présence dans les ordures ménagères permet encore, lors de leur incinération,
d'économiser le fuel nécessaire à leur prise de combustion, améliorant d'autant le
rendement de ces installations.
Le problème vient des
fumées produites lors de la combustion qui peuvent être polluantes. Il faut les traiter
afin déliminer tous les produits toxiques et limiter les poussières. A leur sortie
du four, les fumées sont filtrées pour récupérer tous les produits polluants (chlorure
dhydrogène HCl, produits azotés NOx, produits soufrés SOx
).
Les fumées qui sortent de
lusine ne doivent être composées que de dioxyde de carbone et deau.
Dans toutes les grandes
villes françaises, il existe des usines dincinération des ordures ménagères avec
récupération dénergie, par exemple ci-dessous avec le cas de lusine de
Villefranche sur Saône
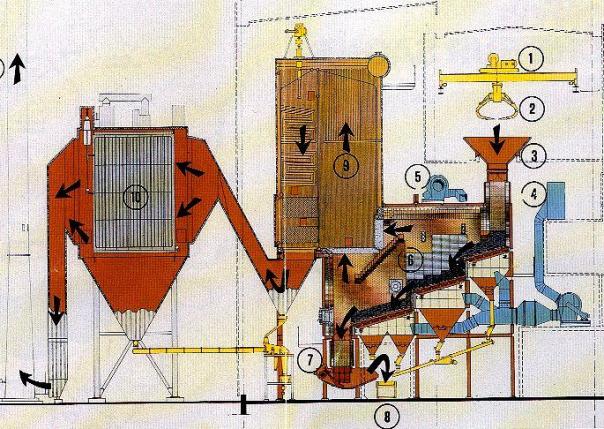
Légende
1)
Pont roulant
2) Grappin
3) Trémie
4) et 5) Arrivées d'air
6) Four
7) Pousseur de scories
8) Plateau vibrant
9) Chaudière de récupération d'énergie
10) Electrofiltre
Les déchets arrivent tous
les jours à l'usine grâce aux camions de ramassage. Ils sont versés dans une grande
fosse (non visible sur le schéma)
·
1)+2) = pont roulant plus grappin.
Le grappin qui est fixé au
pont roulant "ramasse" les déchets (le grappin peut contenir 1 tonne de
déchet).
·
3) La trémie.
Les déchets sont versés
dans la trémie.
·
4) et 5) Arrivées d'air.
Pour que la combustion ait
lieu, le four est alimenté en air. L'air arrive sous le four (4) et au dessus (5).
·
6) Le four.
Les déchets brûlent dans
le four. Cette combustion dégage beaucoup de chaleur.
·
7) Pousseur de scories.
Les déchets non brûlés
(le verre, les métaux) tombent dans une benne. Ils sont poussés vers le plateau vibrant
(8) pour être triés.
·
8) Plateau vibrant.
Les déchets non brûlés
arrivent sur ce plateau vibrant qui les emmène vers un déferrailleur (invisible sur le
schéma). Ce dispositif sert à séparer les métaux ("ferraille") du reste des
déchets (le verre...).
·
9) Chaudière de récupération d'énergie.
La chaleur dégagée par la
combustion des déchets est utilisée pour produire de la vapeur à 200°C. Cette vapeur
("surchauffée") servira à alimenter un réseau de chaleur : la chaleur de la
combustion sert à chauffer des maisons.
·
10) Filtre.
Les fumées
"sales" qui proviennent de la combustion doivent être filtrées. On élimine
une grande partie des poussières et des produits toxiques (HCl, HF...) qui sont produits
lors de la combustion des déchets. Ces poussières sont récupérées et stockées dans
des décharges spéciales.
·
La cheminée.
Ensuite les fumées
"propres" sortent dans l'atmosphère par la cheminée.
I. 4. La valorisation chimique ou valorisation matière première
En complément de la valorisation énergétique et de la
valorisation matière, une troisième technique de recyclage des matières plastiques se
développe, cest la valorisation chimique, recyclage chimique ou valorisation
matière première. Ce procédé, qui fait appel à des traitements chimiques complexes,
commence pour le PET
et reste expérimental pour les autres matériaux plastiques. Compte tenu que ce domaine
dactivité est très récent, il nous a été difficile de développer cette partie
précisément. La valorisation chimique consiste en la transformation d'un objet plastique
usagé en monomères, en pétrole, ou en gaz de synthèse réutilisables comme le montre
le schéma ci-dessous.
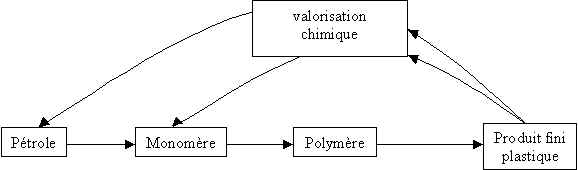
Schéma 1 : La valorisation
chimique
Actuellement, deux techniques de valorisation chimique sont à
létude dans les industries de raffinage et de pétrochimie : la première permet de
revenir au monomère de départ par une dépolymérisation, la seconde va plus loin en
amont et fait revenir les polymères en produits pétrochimiques de base (pétrole ou
naphta).
Les procédés dhydrolyse Tredi et TBI (pilote en fonctionnement à Issoire,
Puy-de-Dôme) se développent actuellement. La valorisation chimique peut également
utiliser la technique de pyrolyse c'est à dire par chauffage sans oxygène (pilote en
Allemagne développé par BASF, et en Écosse), ou de gazéification (pilotes en Allemagne
et aux Pays-Bas). Ces process encore coûteux ne permettent pas à lheure actuelle
un développement industriel. Mais, surtout, la difficulté vient du besoin de retrouver
une résine vierge utilisable, tout en sen différenciant suffisamment pour être
utilisée de préférence à la résine vierge. En effet, bien que techniquement ce type
de recyclage soit possible, le coût de traitement est encore très supérieur au coût de
la résine vierge (de l'ordre de 5 à 6 F, contre 2 à 4 F pour la résine vierge du PET)
car il nécessite des traitements différents selon le type de plastique récupéré et la
mise en place de centres de tri performants. Pour le procédé TBI, le PET dépolymérisé
est transformé en une résine qui sert à la fabrication de mousses polyuréthannes
isolantes. Cette résine prête à l'emploi, peut donc être vendue plus chère que la
résine vierge. Le marché estimé est de 10.000 tonnes en 1999, 25.000 en 2002 (soit la
transformation de 12 à 18.000 tonnes de PET, soit 350 à 550 millions de bouteilles).
Cette dernière solution est prometteuse car le recyclage chimique se positionne sur un
marché qui est lui-même en croissance (le marché des résines polyuréthannes est
estimé à 30.000 tonnes/an et 150.000 tonnes en Europe). Nous avons préférentiellement
parlé du PET car cest un polymère qui est de plus en plus utilisé.
I. 4. 1 La
dépolymérisation
La principale technique envisagée est celle de la
dépolymérisation qui permet de séparer les constituants de base du polymère. De plus,
suivant le type de polymère, on peut le valoriser chimiquement par différentes
techniques.
I. 4. 1. 1
Lhydrolyse
Lhydrolyse est la réaction au cours de laquelle une liaison
chimique est rompue sous l'action de l'eau. Le procédé dhydrolyse permet de
récupérer lacide téréphtalique, avec une
« pureté alimentaire ». Des sociétés américaines (WELLMAN, ENVIPCO) sont déjà en
place, mais des projets français (TREDI, TBI : récupération de polyols pour la
fabrication de mousses) se développent.
·
Le procédé Trédi
Le projet de valorisation chimique suivant le procédé Recopet
repose sur le recyclage chimique des déchets d'emballages en PET. Il est actuellement
conduit par Trédi et utilisé par Polyphénix.
La première phase consiste à broyer et à séparer les déchets
pour en éliminer les impuretés. Puis une réaction chimique (la dépolymérisation)
permet de récupérer les deux constituants de base du PET. Une opération finale élimine
les colorants et les dernières impuretés encore présentes. Les produits obtenus, d'un
degré de pureté comparable à celui des produits de première synthèse, permettent leur
utilisation dans les mêmes conditions que les matières premières vierges.
La faisabilité de cette technique, testée d'abord en laboratoire,
a également été validée au niveau industriel. L'avantage de ce procédé est qu'il
permet de recycler des déchets plastiques souillés et/ou mélangés, même à de fortes
proportions (jusqu'à 10 % d'impuretés et de résines étrangères) sans avoir à
effectuer des sur tris poussés.
·
Le procédé TBI
Ce projet concerne également la valorisation chimique du PET mais
les produits obtenus après réaction sont différents : des produits de base comme le
méthanol qui pourra être utilisé comme combustible et des composants synthétiques d'un
autre polymère, le polyuréthanne (PU). Plus régulières, les mousses de PU obtenues à
partir de ces composés présentent d'excellentes propriétés thermiques et
dimensionnelles. Une unité de
pré-industrialisation fonctionne depuis maintenant un an. Des modifications techniques
ont été effectuées afin d'améliorer encore le procédé.
Si les deux techniques présentées, considérées comme
techniquement possibles, paraissent attrayantes au vu des importants tonnages
prévisionnels traités, elles restent peu développées aujourd'hui. L'équipement
industriel nécessaire à une telle valorisation est lourd et accessible à peu de
structures. La rentabilité économique reste également à trouver. L'intérêt d'une
telle valorisation est néanmoins considérable puisqu'elle permettrait d'alléger
certaines contraintes de qualité qui pèsent actuellement sur les collectivités.
I. 4. 1. 2 Autres
méthodes de dépolymérisation
Il existe divers procédés qui permettent de revenir aux monomères
de base par dépolymérisation. Ces procédés sont utilisés pour des polymères de
polycondensation pur et sont empruntés à des méthodes classiques de réactions
chimiques connues dans le cadre général de la chimie organique. Cependant en utilisant
des conditions expérimentales adaptées à certains types de polymères, on peut les
appliquer et ainsi revenir aux monomères de base. Outre lhydrolyse qui est
également une technique permettant le retour au monomère de base, nous trouvons :
Ø Lalcoolyse
Ø La
glycolyse
Ø La
saponification
Cependant, ces procédés étant très récents, il nous a été
difficile de trouver des documents techniques concernant ces derniers et cest la
raison pour laquelle nous nous contenterons de ne donner que le nom de ces techniques.
I. 4. 2 Techniques
permettant le retour aux produits pétrochimiques de base
Ces techniques sont utilisées pour des polymères obtenus par
polyaddition (PVC, PP, PE). Lobjectif est la décomposition des macromolécules
constituantes des résines en matières premières utilisables à nouveau dans les
raffinerie, la pétrochimie et la chimie.
I. 4. 2. 1 La
thermolyse (ou pyrolyse)
La thermolyse (ou pyrolyse) est un procédé thermique de traitement
des matières organiques en absence dair (la différence entre les deux
dénominations tient au mode de chauffage) convenant même pour les plastiques souillés
(jusquà 20 %). Les molécules ne sont pas transformées par oxydation comme dans le
cas de la combustion, mais leurs constituants chimiques sont séparés sous leffet
de la chaleur, à une température variant de 400 à 700°C (craquage). La
chaleur et l'absence d'air entraînent une décomposition des matières organiques en deux parties :
Ø Un
combustible solide (ressemblant à du coke)
Ø et
un combustible gazeux (comportant notamment du CO2, du méthane, du CO, et de
lhydrogène).
Ces deux combustibles peuvent alors être brûlés dans
lunité même (on parle de thermolyse intégrée), ou être utilisés comme
combustibles de substitution dans une autre installation. Dans tous les cas, la thermolyse
consiste en une première transformation des déchets pour quils puissent être
valorisés énergétiquement ensuite.
·
Avantages
Ø Production
dun combustible alternatif qui peut remplacer les combustibles fossiles non
renouvelables.
Ø Pas
de rejets gazeux pendant la phase de thermolyse mais uniquement lors de lutilisation
des combustibles produits.
Ø La
taille modulable des unités et une souplesse dutilisation. Les fours peuvent en
effet tourner de 40 à 125% de leur capacité nominale, ce qui permet de suivre les
variations de production de déchets. Contrairement aux incinérateurs qui doivent
recevoir toujours la même quantité de déchets pour pouvoir fonctionner correctement.
Ø De
petites unités peuvent être dispersées sur lensemble du territoire, ce qui permet
leur installation près des endroits où l'on a besoin des combustibles alternatifs et
près des lieux de production de déchets. Conséquence : limitation du transport des
déchets sur de longues distances et meilleure répartition des risques et des nuisances
pour la population.
Ø Des
études sont encore en cours, mais cette technique semble globalement moins chère que
lincinération en masse.
·
Inconvénients
Ø Cette
méthode comporte donc des avantages par rapport à lincinération et la
valorisation thermique mais elle est aussi plus exigeante. En effet, la qualité du coke
produit est directement liée à la composition des déchets qui sont crackés. Il faut
donc bien les trier avant.
Ø Dautre
part, cette méthode névite pas la production de résidus dangereux qui doivent
être mis en décharge de classe 1 (0,1 à 3% des déchets entrants). Dautres
résidus inertes sont également produits (15 à 20% des déchets entrants), tout comme
dans le procédé dincinération classique.
Différents systèmes de thermolyse sont actuellement étudiés et
testée un peu partout en Europe. Enfin, les unités de thermolyse en service ont des
capacités à partir de 1 t/h jusqu'à 8 t/h mais, actuellement, la société THERMOSELECT
construit une unité de 30 t/h à Karlsruhe.
I. 4. 2. 2 Le
craquage
Le craquage est une opération de conversion du pétrole consistant
en la transformation des hydrocarbures le constituant en molécules plus petites, à
points d'ébullition inférieurs. Le craquage permet d'obtenir des bases d'essence à haut
indice doctane. La coupure des
liaisons des alcanes notamment et leurs réarrangements se produisent, sous le seul effet
de la température (craquage thermique), ou
par action de la vapeur (vapocraquage), de
l'hydrogène (hydrocraquage : craquage à
haute température et à haute pression par hydrogénation
catalytique), de la pression, d'un catalyseur (craquage
catalytique). Les produits obtenus par craquage sont des oléfines (propylène,
éthylène, butadiène), des aromatiques,
Lopération dite de vapocraquage
consiste à casser les molécules de la charge, par pyrolyse, pour obtenir des
molécules plus petites. De plus, il est réalisé en présence de vapeur d'eau qui sert
à diluer les hydrocarbures pour éviter les réactions parasites d'aromatisation des
cycloalcanes aboutissant à la formation de goudrons et de coke par condensation. On
utilise entre 0,25 et 1 tonne de vapeur deau par tonne d'hydrocarbure à craquer. La
charge peut être lourde (gazoles), moyenne (naphta) ou légère (éthane, propane,
butane). Les conditions opératoires et la composition du produit obtenu dépendent de la
nature de la charge. Cette technique permet donc dextraire toute une série de molécules chimiques avec
l'action de la vapeur. On extrait par exemple :
Ø Pour
le PE, l'éthylène,
Ø Pour
le PET, l'éthylène glycol (alcool dérivé de
l'éthylène) et l'acide téréphtalique
Ø Pour
le PP, le propène ou propylène
Ø Pour
le PVC, le chlore, isolé à partir du sel ou
de l'acide chlorhydrique est combiné avec l'éthylène
Lhydrocraquage est un procédé de craquage sous hydrogène
permettant généralement dans le raffinage des pétroles bruts, de convertir un distillat
sous vide en produits plus légers hautement plus valorisations.
I. 4. 2. 3
gazéification
Tout comme la pyrolyse, la gazéification est un traitement de
décomposition thermique des résidus. La réaction s'opère en présence limitée
d'oxygène. La température y est cependant plus élevée, soit de 1400 °C à 1500 °C,
ce qui détruit totalement les composés
organiques. La réaction ne produit que du gaz valorisable et des cendres qui peuvent
être toxiques.
Un exemple de ce procédé est le procédé Pyromex qui propose une
solution complète alliant l'élimination efficace et la valorisation économique, sans
résidus, ni émissions. Ce procédé se déroule en 3 phases.
Après une première phase de tri et de conditionnement, une
deuxième phase de broyage et de solidification lui succède, la troisième et dernière
phase qui est celle de la gazéification.
La gazéification à température ultra haute est la distillation
destructrice du matériel organique. Ce processus de distillation exige l'application
d'une intense énergie thermique indirecte, en l'absence d'oxygène, qui réduit le
matériel à des gaz combustibles et à des matériaux inorganiques, non nuisibles et qui
ne lessivent pas. L'installation de gazéification réduit efficacement les composants
organiques constitués de déchets urbains ou toxiques.
Le pyro-convertisseur fonctionne à des températures ultra hautes,
dans une atmosphère dépourvue d'oxygène. Les températures ultra hautes, dépassant 2
000 C° sont atteintes moyennant l'emploi du réacteur à induction, système innovateur
breveté. Le produit final, le pyrosilate, est un matériau inorganique inerte, qui ne
lessive pas et n'est pas nuisible à l'environnement. Le produit vaporisé (gaz) est
retraité dans un post-brûleur, qui nettoie les vapeurs et élimine les gaz toxiques. Ce
post-brûleur a la fonction d'un désinfecteur thermique.
De configuration modulaire, elle peut s'adapter à des débit de 25
à plus de 1 000 tonnes par jour. Le produit final ne lessive pas et peut être stocké en
toute sécurité. Il peut également être converti en matériaux de construction ou
encore être formé en briquettes d'énergie, transportables et facilement entreposables.
Un pilote industriel est en démonstration à Brentwood, Angleterre.
PolyEthylène Téréphtalate
Fraction légère du pétrole distillé
caractérise la tendance à la détonation d'un carburant
Réaction de combinaison avec l'hydrogène, d'addition de dihydrogène sur un composé
insaturé
Page précédente - Page suivante
|