III La Métallurgie des Poudres
1 Procédé dobtention
dune pièce frittée
La formation dun compose fritté commence par la densification de la poudre
métallique dans une matrice rigide ayant une cavité de contour plus ou moins complexe.
Dans cette opération, de hautes pressions sont exercées sur la poudre dans la cavité de
la matrice, simultanément par le dessous et le dessus, via plusieurs poinçons de
compression se déplaçant verticalement. La pression permet aux surfaces des particules
de poudre de sinterpénétrer opérant ainsi une sorte de soudure à froid entre les
surfaces. Après léjection, les pièces sont suffisamment solides pour permettre
une manipulation ultérieure.
A Elaboration de la pièce frittée
Une pièce frittée est obtenue grâce à une matière première sous forme de
poudre qui est comprimée, frittée puis traitée. Nous allons détailler ces différentes
phases pour comprendre le moyen dobtenir une pièce selon les caractéristiques
voulues.
1 La compression
Lavantage des pièces frittées vient en partie de leur tenue mécanique.
Cette particularité est due à la phase de compression. Cest en effet cette phase
qui permet la densification de la poudre et délimite ainsi ses caractéristiques
techniques telles que lélasticité ou la dureté. La densification de la pièce est
due à la déformation plastique des particules de poudre qui adaptent leurs contours aux
particules adjacentes formant ainsi une structure liée.
La poudre est comprimée grâce à des presses de puissances différentes. La
machine de compression est choisie en fonction des caractéristiques à obtenir mais aussi
en fonction de la taille de la pièce à réaliser. La poudre de fer est achetée par
tonne pour négocier les meilleurs prix. Un mixer bi-conique permet au poudrier de faire
les mélanges voulus. Une deuxième solution est de plus en plus employée par la
société : la commande directe de sacs de mélange.
Le cycle de compression peut être divisé en trois étapes :
-
le remplissage de la matrice
-
la densification de la poudre
-
lextraction du comprimé de
la matrice
Chacune de ces
trois étapes est caractérisée par des positions ou des mouvements spécifiques des
parties individuelles de loutil.
2 Le remplissage
La poudre tombe ou
sécoule par sa propre gravité depuis le dispositif de remplissage jusquà la
cavité de la matrice. Les particules poudre doivent être de faible taille pour garantir
une bonne coulabilité et un remplissage satisfaisant. En effet, si les particules font
des pontages entre elles, un remplissage irrégulier se produit. Des manques de matière
sur la pièce finale en résultent alors.
Pour une pièce de
forme ambiguë, il faut faire attention à la tenue à vert. En effet, si le remplissage
nest pas régulier, la densification ne sera pas la même en tout point. Il faudra
alors compenser ce phénomène par la pression de compression ou le mode compression.
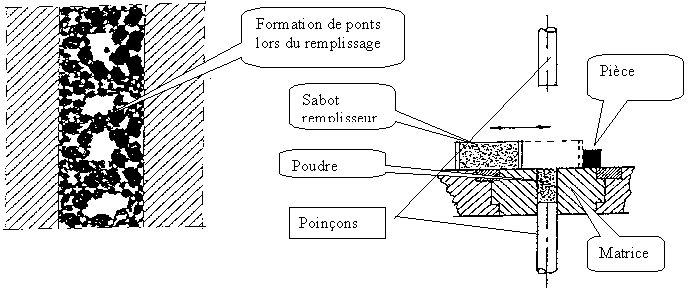
3 Densification de la poudre
Du fait des frottements entre la poudre et les parois de la matrice, les comprimés
sont plus denses à leurs deux extrémités près des poinçons de compression mobiles,
quà leur centre. Le lieu de plus basse densité doit apparaître à mi-chemin entre
le sommet et le bas du comprimé. Ceci nest possible que si les poinçons se
déplacent symétriquement par rapport à la matrice de compression. Ces mouvements sont
obtenus de trois façons différentes.
a)
- premier principe : poinçon à déplacement
symétrique
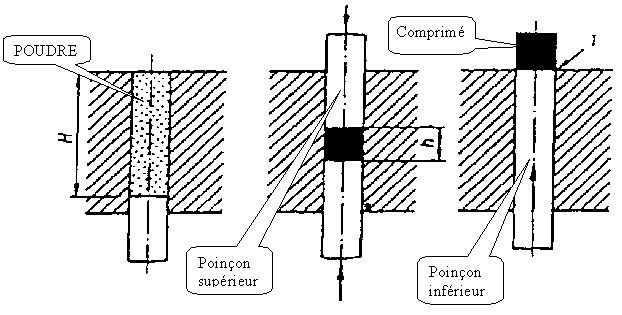
La matrice et la
broche centrale ne changent pas de position au cours de la densification de la poudre.
Pendant léjection, la broche centrale reste dans le comprimé jusqu'à ce que celui
ci ait quitté la matrice et quil soit détendu élastiquement. Ensuite la broche
centrale est retirée sans frottement. (voir schéma suivant)
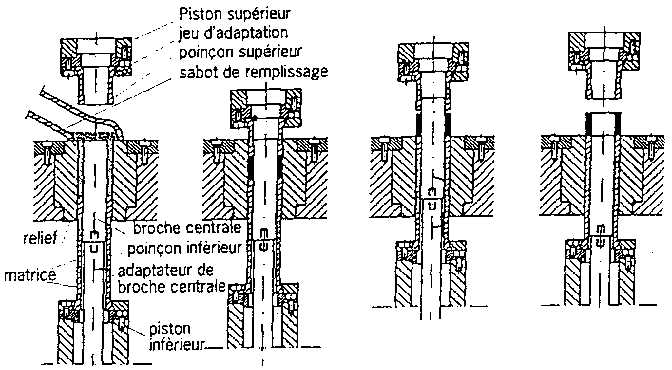
b)
- Second principe avec matrice
« Flottante »
Le processus de la
matrice flottante ne demande que deux simples fonctions dune presse : un
mouvement vers le bas généré par un piston supérieur capable dexercer de grande
force, et un mouvement vers le bas généré par un piston inférieur capable
dexercer des forces inférieures aux précédentes. Linconvénient dun
tel système est que le mouvement de la matrice pendant la densification est entièrement
généré par des forces de frottement qui sont incontrôlables puisquelles sont
lourdement influencées par les variations de la teneur en lubrifiant de la poudre, par
les variations de températures de la matrice pendant la production, et par lusure
progressive des parois de la matrice.
c)
Troisième principe : variation des vitesses de
poinçon
Le poinçon de
droite est, via une tige de connexion, soulevé à sa position de remplissage par un
ressort. Pendant la phase de compression, le piston inférieur de la presse abaisse le
plateau de la matrice à la moitié de la vitesse du poinçon supérieur, tandis que le
poinçon inférieur de gauche reste sur le plateau de base immobile de ladaptateur.
Sous leffet de laugmentation de pression dans la poudre densifiée, le
poinçon inférieur droit se déplace vers le bas, contre la force du ressort de support,
jusqu'à ce quil repose sur le porte outil. Après compression, le piston inférieur
de la presse continue à tirer le plateau de la matrice vers le bas, et le coin attaché
au plateau de la matrice force le porte outil de côté. Le poinçon inférieur droit,
cette fois non supporté, suit le panneau de la matrice vers le bas jusqu'à ce que le
comprimé soit complètement sorti de loutil de compression. (voir schéma)
4 - Extraction du comprimé de la matrice
A la fin de la phase de compression, la matrice et les poinçons inférieurs sont
déplacés lun par rapport à lautre de telle sorte que le comprimé soit
poussé vers la sortie de la matrice. Pour obtenir cet effet, il importe peu que la
matrice soit immobile et que les poinçons se déplacent ou vice versa. Limportant
est que, durant ce processus, les poinçons inférieurs ne bougent pas lun par
rapport à lautre pour éviter la création de fissures dans le comprimé.
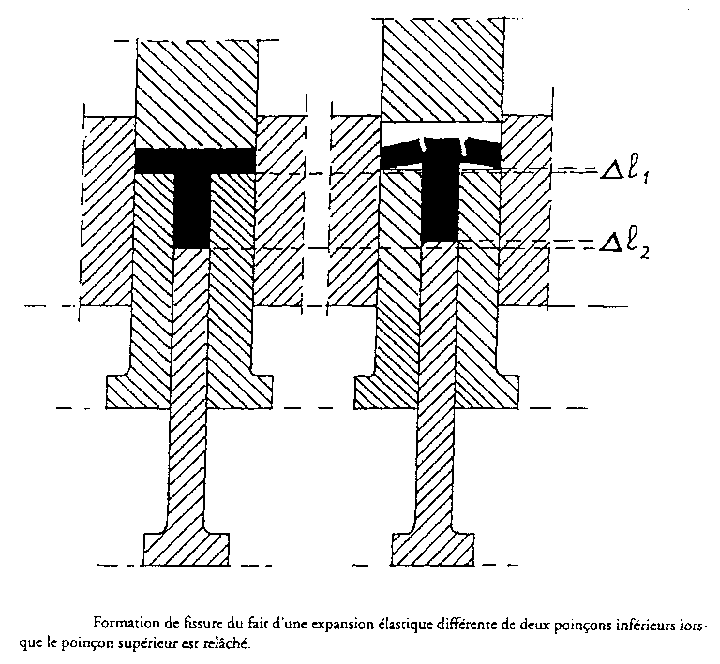
5 - Le frittage
a) - Les paramètres
le procédé de
frittage est régi par 5 paramètres :
- le temps et
la température
Plus la température est haute, plus court est le temps de frittage nécessaire
pour atteindre le degré désiré de liaison entre les particules de poudre comprimée.
Ceci constitue un dilemme car du point de vue de lefficacité en production, un
temps de frittage plus court serait préférable mais cela implique de hautes
températures de frittage donc un frittage moins économique du fait dun coût de
maintenance des fours plus élevé.
- La
structure géométrique des particules de poudre.
A condition de
frittage donné, les poudres fines ou à grandes surfaces spécifiques frittent plus vite
que les poudres compactes plus grosses. Le dilemme est que les poudres plus fines sont
plus difficiles à comprimer que les grosses, et les comprimés faits à partir de poudres
plus fines ont un retrait plus important au frittage que ceux conçus avec les poudres
plus grosses.
- Condition
de mélange des poudres
Les composants
dun mélange de poudre sont sélectionnés en type et quantité dans le but
datteindre les propriétés physiques désirées et les changements dimensionnels
contrôlés pendant le frittage. Lors du frittage, un alliage des composants va se
produire. A la température de frittage usuelle (1150 °C), les processus dalliages
sont lents et lhomogénéisation des éléments dalliage nest pas
atteinte. Mais si la poudre contient un élément dont la température de fusion est
inférieure à celle de frittage alors sa phase liquide va accélérer le processus
dalliage.
- La densité
des comprimés de poudres.
Plus la densité
dun comprimé est grande, plus la surface de contact entre les particules de poudres
est importante, et plus les processus de liaisons et dalliages sont efficaces.
- Composition
de l'atmosphère protectrice du four de frittage.
Latmosphère protectrice doit remplir plusieurs fonctions pendant le
frittage. Elle doit protéger les pièces à fritter de loxydation et réduire le
plus possible la présence doxydes résiduels. Elle doit également prévenir la
décarburation des matériaux contenant du carbone, et, vice versa, empêcher la
carburation de matériaux exempts de carbone. Dans la métallurgie des poudres de fer, les
atmosphères sont de trois types :
-
Type
réductrice-décarburante : Hydrogène (H2), Ammoniac dissocié
-
Type réductrice-carburante :
endogaz
-
Type neutre : Azote
cryogénique, avec addition mineure dHydrogène
b) - le four
Le four est
loutil majeur du frittage car cest lui qui va permettre dobtenir les
trois types datmosphères décrites précédemment.
Un four en continu
de conception récente, pour le frittage de pièces mécaniques en poudre de fer, se
compose habituellement de quatre zones dutilité différentes :
1
la zone de délubrification où les lubrifiants sont brûlés entre 250 et 300°C
2 la zone chaude où les pièces en poudre de fer sont frittées à
1120-1150°C
3 la zone de restauration du carbone où les pièces décarburées
superficiellement peuvent être recarburées à 800-900°C
4 la zone de refroidissement où les pièces frittées sont refroidies
jusqu'à environ 150-250 °C, avant dêtre mises à lair.
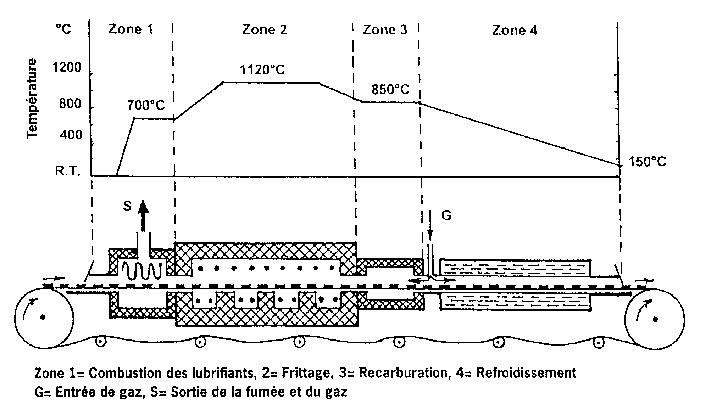
Dans lidéal, chaque zone aurait besoin de sa propre combinaison de débit,
direction et composition de latmosphère. Mais, ces conditions idéales ne peuvent
pas être atteintes.
Si les fours ne sont pas
correctement élaborés ou réglés, des problèmes thermodynamiques se produisent. Des
défauts de forme ou des déficiences mécaniques de la pièce en résultent
Page précédente -
Page suivante |